Przed zakupieniem bielizny warto dowiedzieć się, jaki kształt będzie najlepiej podkreślał walory naszej figury. Perfekcyjnie…
Jak połączyć dwa kompresory?
Łączenie dwóch kompresorów to proces, który wymaga staranności i zrozumienia podstawowych zasad działania tych urządzeń. Przede wszystkim, przed przystąpieniem do jakichkolwiek działań, należy upewnić się, że oba kompresory są kompatybilne pod względem technicznym. Ważne jest, aby miały podobne parametry robocze, takie jak ciśnienie maksymalne oraz wydajność. Różnice w tych parametrach mogą prowadzić do nieefektywnej pracy lub uszkodzenia sprzętu. Kolejnym krokiem jest zaplanowanie układu połączeń. W przypadku łączenia kompresorów można zastosować różne metody, takie jak połączenie równoległe lub szeregowe. Połączenie równoległe pozwala na zwiększenie wydajności, podczas gdy połączenie szeregowe może być użyteczne w sytuacjach wymagających wyższego ciśnienia. Niezależnie od wybranej metody, kluczowe jest zapewnienie odpowiedniej wentylacji oraz zabezpieczeń przed przeciążeniem. Warto również zainwestować w odpowiednie złączki i węże, które będą odporne na wysokie ciśnienie i temperaturę.
Jakie narzędzia są potrzebne do łączenia kompresorów?
Przy łączeniu dwóch kompresorów niezbędne jest posiadanie odpowiednich narzędzi oraz materiałów, które zapewnią bezpieczeństwo i efektywność całego procesu. Na początek warto zaopatrzyć się w zestaw kluczy i śrubokrętów o różnych rozmiarach, które umożliwią montaż elementów oraz regulację połączeń. Dobrze jest również mieć pod ręką wkrętarkę elektryczną, co znacznie przyspieszy pracę. Kolejnym ważnym elementem są złączki i węże pneumatyczne, które powinny być dostosowane do specyfikacji obu kompresorów. Warto zwrócić uwagę na ich jakość oraz odporność na wysokie ciśnienie. Dodatkowo przydatnym narzędziem będzie manometr, który pozwoli na monitorowanie ciśnienia roboczego w systemie. Nie można zapomnieć o środkach ochrony osobistej, takich jak rękawice czy okulary ochronne, które zapewnią bezpieczeństwo podczas pracy z urządzeniami pneumatycznymi. Jeśli planujesz bardziej skomplikowane połączenia elektryczne między kompresorami, konieczne może być również posiadanie multimetru oraz podstawowej wiedzy z zakresu elektryki.
Jakie są zalety łączenia dwóch kompresorów?
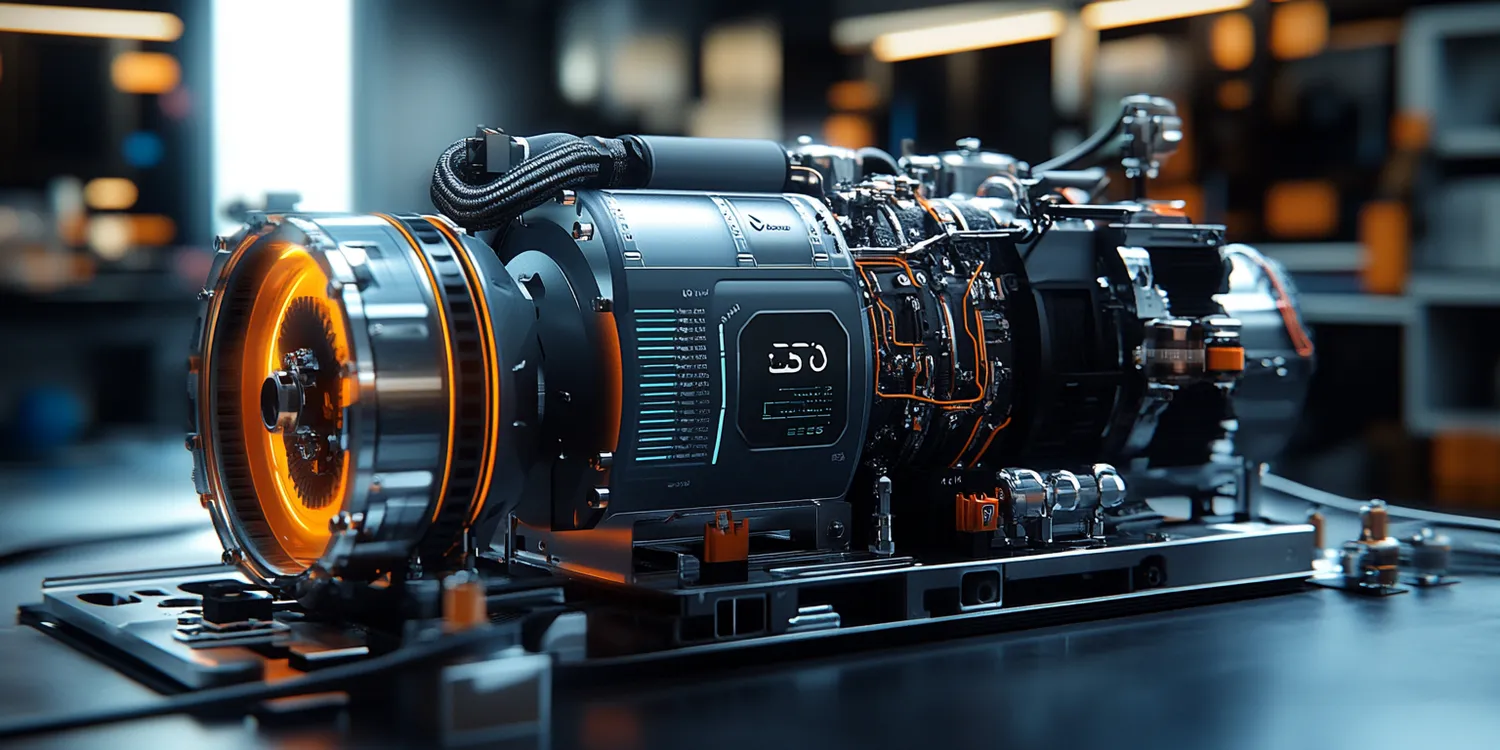
Jak połączyć dwa kompresory?
Łączenie dwóch kompresorów niesie ze sobą wiele korzyści, które mogą znacząco wpłynąć na efektywność pracy w różnych zastosowaniach przemysłowych oraz domowych. Przede wszystkim, dzięki połączeniu dwóch jednostek można zwiększyć ogólną wydajność systemu pneumatycznego. To oznacza, że użytkownik może uzyskać większą ilość sprężonego powietrza w krótszym czasie, co jest szczególnie istotne w przypadku intensywnego użytkowania narzędzi pneumatycznych. Ponadto łączenie kompresorów pozwala na uzyskanie wyższego ciśnienia roboczego, co może być niezbędne w specyficznych aplikacjach wymagających dużej mocy. Kolejną zaletą jest możliwość optymalizacji kosztów eksploatacyjnych; zamiast inwestować w jeden duży kompresor o wysokiej wydajności, można wykorzystać dwa mniejsze urządzenia, co często okazuje się bardziej ekonomiczne. Dodatkowo łączenie kompresorów zwiększa elastyczność systemu; jeśli jeden z nich ulegnie awarii, drugi nadal może funkcjonować samodzielnie, co minimalizuje przestoje w pracy.
Jakie problemy mogą wystąpić przy łączeniu kompresorów?
Podczas łączenia dwóch kompresorów istnieje kilka potencjalnych problemów, które mogą wpłynąć na efektywność działania całego systemu. Jednym z najczęstszych błędów jest niewłaściwe dobranie parametrów technicznych obu urządzeń; różnice w ciśnieniu roboczym czy wydajności mogą prowadzić do nieefektywnej pracy lub wręcz uszkodzenia jednego z kompresorów. Innym problemem mogą być nieszczelności w połączeniach; niewłaściwie zamontowane złączki czy uszczelki mogą powodować utratę sprężonego powietrza i obniżać wydajność systemu. Warto również zwrócić uwagę na kwestie związane z wentylacją; oba kompresory muszą mieć zapewniony odpowiedni dostęp powietrza do chłodzenia, inaczej mogą przegrzewać się i ulegać awariom. Dodatkowo konieczne jest monitorowanie obciążenia elektrycznego; jeśli jeden z kompresorów będzie pracował intensywniej niż drugi, może to prowadzić do przeciążenia układu elektrycznego i wyzwolenia zabezpieczeń.
Jakie są najlepsze praktyki przy łączeniu kompresorów?
Aby proces łączenia dwóch kompresorów przebiegł sprawnie i efektywnie, warto zastosować kilka najlepszych praktyk, które pomogą uniknąć problemów oraz zwiększyć wydajność całego systemu. Przede wszystkim, przed przystąpieniem do jakichkolwiek działań, należy dokładnie zaplanować cały projekt. Obejmuje to nie tylko wybór odpowiednich kompresorów, ale także ustalenie ich lokalizacji oraz układu połączeń. Ważne jest, aby oba urządzenia były umieszczone w dobrze wentylowanym miejscu, co pozwoli na ich efektywne chłodzenie podczas pracy. Kolejnym krokiem jest dokładne sprawdzenie wszystkich elementów instalacji, takich jak złączki, węże i uszczelki, aby upewnić się, że są one odpowiednie do zastosowań przemysłowych i wytrzymałe na wysokie ciśnienie. Warto również zainwestować w system monitorowania ciśnienia oraz przepływu powietrza, co pozwoli na bieżąco kontrolować parametry pracy kompresorów. Regularna konserwacja obu jednostek jest kluczowa; zaleca się przeprowadzanie przeglądów co najmniej raz na kilka miesięcy, aby zidentyfikować ewentualne problemy zanim staną się poważne.
Jakie są różnice między połączeniem równoległym a szeregowym kompresorów?
Decyzja o tym, czy połączyć dwa kompresory równolegle czy szeregowo, ma kluczowe znaczenie dla efektywności całego systemu pneumatycznego. Połączenie równoległe polega na tym, że oba kompresory pracują jednocześnie, co pozwala na zwiększenie wydajności sprężonego powietrza bez podnoszenia ciśnienia roboczego. Taki układ jest idealny w sytuacjach, gdy potrzebna jest duża ilość powietrza do zasilania narzędzi pneumatycznych lub innych urządzeń wymagających dużego przepływu. Z drugiej strony połączenie szeregowe umożliwia uzyskanie wyższego ciśnienia roboczego poprzez podłączenie drugiego kompresora do wyjścia pierwszego. Taki układ jest korzystny w aplikacjach wymagających dużych ciśnień, takich jak malowanie natryskowe czy prace w warsztatach mechanicznych. Warto jednak pamiętać, że połączenie szeregowe może być bardziej skomplikowane w instalacji i wymaga starannego dobrania parametrów obu urządzeń.
Jakie są najczęstsze błędy przy łączeniu kompresorów?
Podczas łączenia dwóch kompresorów można napotkać wiele pułapek i błędów, które mogą prowadzić do problemów z działaniem całego systemu. Jednym z najczęstszych błędów jest niewłaściwe dobranie parametrów technicznych obu urządzeń; różnice w wydajności czy ciśnieniu roboczym mogą prowadzić do nieefektywnej pracy lub uszkodzenia jednego z kompresorów. Kolejnym powszechnym problemem jest brak odpowiednich zabezpieczeń przed przeciążeniem; jeśli jeden z kompresorów będzie pracował intensywniej niż drugi, może to prowadzić do jego szybkiego zużycia lub awarii. Niezrozumienie zasad działania układu pneumatycznego również może być przyczyną wielu kłopotów; brak wiedzy na temat obiegu powietrza oraz ciśnień roboczych może skutkować nieefektywną pracą systemu. Ponadto zaniedbanie regularnej konserwacji obu jednostek może prowadzić do gromadzenia się zanieczyszczeń oraz uszkodzeń komponentów wewnętrznych. Ważne jest również stosowanie wysokiej jakości materiałów i akcesoriów; tanie złączki czy węże mogą szybko ulegać uszkodzeniom i powodować nieszczelności w systemie.
Jakie zastosowania mają połączone kompresory w przemyśle?
Połączone kompresory znajdują szerokie zastosowanie w różnych dziedzinach przemysłu, gdzie wymagane są zarówno duże ilości sprężonego powietrza, jak i wysokie ciśnienie robocze. W branży budowlanej połączone kompresory są często wykorzystywane do zasilania narzędzi pneumatycznych takich jak młoty udarowe czy wiertarki udarowe. Dzięki zwiększonej wydajności możliwe jest efektywne wykonywanie prac budowlanych nawet w trudnych warunkach. W przemyśle motoryzacyjnym połączone kompresory służą do malowania natryskowego oraz innych procesów wymagających precyzyjnego dostarczania sprężonego powietrza pod wysokim ciśnieniem. Dodatkowo w zakładach produkcyjnych połączone kompresory mogą być używane do zasilania maszyn produkcyjnych oraz systemów automatyki przemysłowej. W branży spożywczej sprężone powietrze jest wykorzystywane do pakowania produktów oraz transportu materiałów sypkich. Połączone kompresory zapewniają nie tylko większą wydajność, ale także elastyczność w dostosowywaniu parametrów pracy do zmieniających się potrzeb produkcji.
Jakie są koszty związane z łączeniem dwóch kompresorów?
Koszty związane z łączeniem dwóch kompresorów mogą się znacznie różnić w zależności od wielu czynników, takich jak rodzaj używanych urządzeń, materiały potrzebne do instalacji oraz skomplikowanie samego procesu montażu. Na początku warto zwrócić uwagę na koszt zakupu dwóch kompatybilnych kompresorów; ceny mogą się znacznie różnić w zależności od producenta oraz specyfikacji technicznych urządzeń. Dodatkowo należy uwzględnić wydatki na akcesoria takie jak złączki, węże pneumatyczne oraz manometry; te elementy są kluczowe dla prawidłowego funkcjonowania całego systemu i ich jakość ma bezpośredni wpływ na bezpieczeństwo i efektywność pracy. Koszty robocizny również powinny być brane pod uwagę; jeśli planujesz zatrudnić specjalistę do wykonania instalacji, warto wcześniej uzyskać kilka ofert cenowych od różnych firm zajmujących się tego typu usługami. Nie można zapominać o przyszłych kosztach eksploatacyjnych związanych z użytkowaniem dwóch kompresorów; regularna konserwacja oraz ewentualne naprawy mogą generować dodatkowe wydatki w dłuższej perspektywie czasowej.
Jakie są alternatywy dla łączenia dwóch kompresorów?
Jeśli łączenie dwóch kompresorów nie jest najlepszym rozwiązaniem dla Twoich potrzeb, istnieje wiele alternatyw, które mogą okazać się równie skuteczne lub nawet lepsze w danym kontekście. Jednym z najpopularniejszych rozwiązań jest zakup jednego większego kompresora o wyższej wydajności i ciśnieniu roboczym; takie urządzenie często oferuje lepszą efektywność energetyczną i mniejsze ryzyko awarii niż dwa mniejsze modele pracujące razem. Inną opcją jest wykorzystanie sprężarek o zmiennej wydajności; te nowoczesne urządzenia dostosowują swoją moc do aktualnych potrzeb użytkownika, co pozwala na oszczędność energii i zmniejszenie kosztów eksploatacyjnych.