Destylarki do rozpuszczalników to urządzenia, które wykorzystują proces destylacji do oddzielania różnych substancji chemicznych. Proces…
Destylarka do rozpuszczalników
Destylarka do rozpuszczalników to urządzenie, które wykorzystuje proces destylacji w celu oddzielenia różnych składników chemicznych od siebie. Działa na zasadzie podgrzewania cieczy, co powoduje jej parowanie, a następnie skraplanie pary w osobnym zbiorniku. Proces ten jest niezwykle efektywny w przypadku substancji o różnych temperaturach wrzenia, co pozwala na uzyskanie czystych frakcji rozpuszczalników. Destylarki są szeroko stosowane w laboratoriach chemicznych, przemyśle farmaceutycznym oraz w produkcji kosmetyków. Dzięki możliwości separacji substancji, destylarki przyczyniają się do zwiększenia wydajności procesów produkcyjnych oraz poprawy jakości finalnych produktów. Warto również zauważyć, że nowoczesne destylarki często wyposażone są w zaawansowane systemy monitorowania i kontroli, co pozwala na precyzyjne dostosowanie parametrów procesu do specyficznych potrzeb użytkownika.
Jakie są rodzaje destylarek do rozpuszczalników dostępnych na rynku
Na rynku dostępnych jest wiele rodzajów destylarek do rozpuszczalników, które różnią się zarówno konstrukcją, jak i przeznaczeniem. Wśród najpopularniejszych modeli wyróżnia się destylarki laboratoryjne, które są zazwyczaj mniejsze i przeznaczone do użytku w laboratoriach badawczych. Charakteryzują się one wysoką precyzją oraz możliwością destylacji niewielkich ilości substancji. Innym typem są destylarki przemysłowe, które są znacznie większe i przystosowane do ciągłej produkcji na dużą skalę. Te urządzenia często posiadają zautomatyzowane systemy sterowania, co pozwala na optymalizację procesów produkcyjnych. Warto również wspomnieć o destylarkach mobilnych, które można łatwo przenosić i używać w różnych lokalizacjach.
Jakie materiały są wykorzystywane w budowie destylarek
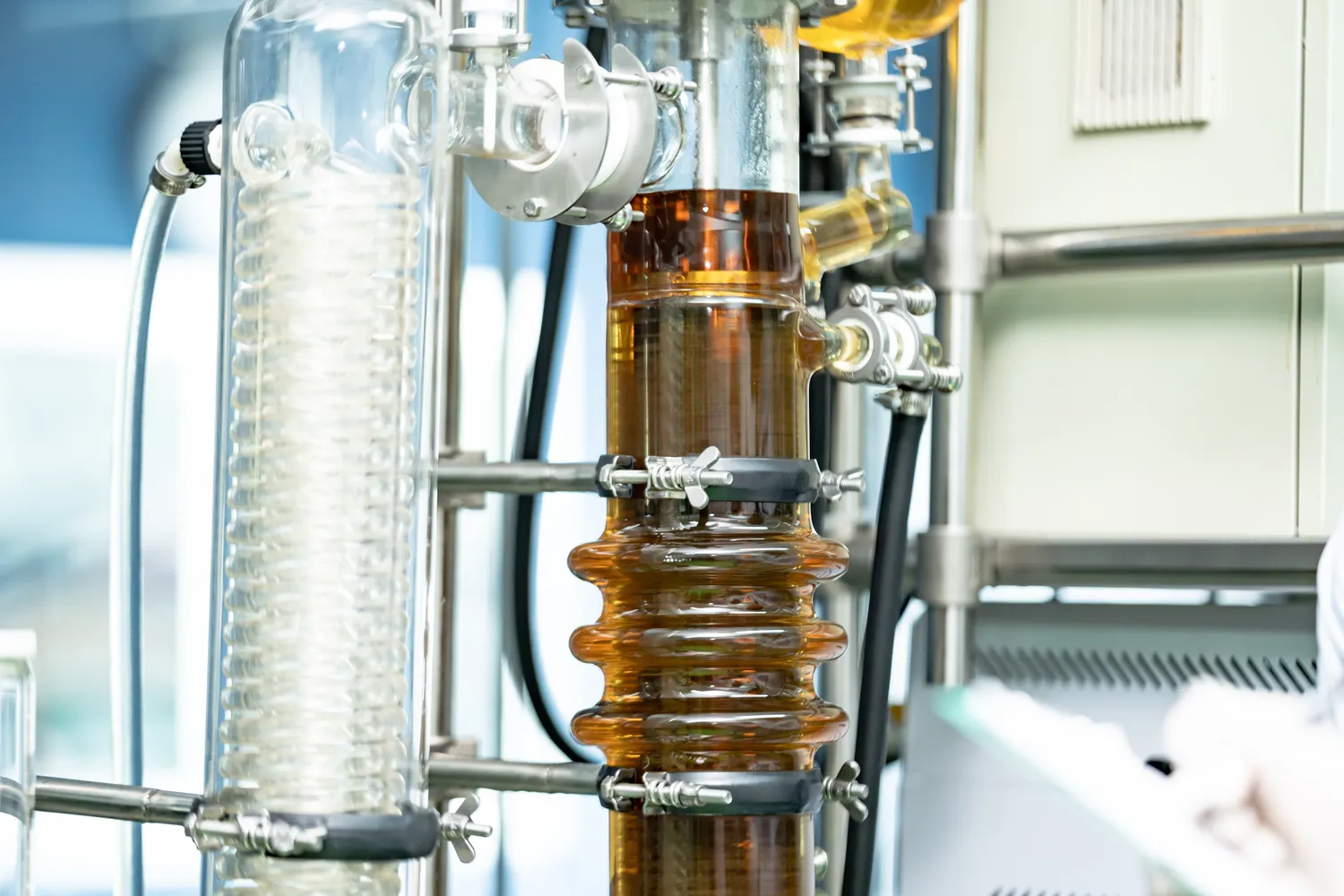
Destylarka do rozpuszczalników
Budowa destylarek do rozpuszczalników opiera się na zastosowaniu różnych materiałów, które muszą spełniać określone normy dotyczące odporności chemicznej oraz termicznej. Najczęściej wykorzystywanym materiałem jest stal nierdzewna, która charakteryzuje się wysoką odpornością na korozję oraz trwałością. Dzięki tym właściwościom stal nierdzewna jest idealnym wyborem dla urządzeń pracujących z agresywnymi substancjami chemicznymi. Inne materiały to szkło borokrzemowe, które jest stosowane w mniejszych destylarkach laboratoryjnych ze względu na swoją przejrzystość oraz odporność na wysokie temperatury. W niektórych modelach można spotkać także elementy wykonane z teflonu lub innych tworzyw sztucznych, które są odporne na działanie wielu chemikaliów.
Jakie są kluczowe czynniki przy wyborze destylarki do rozpuszczalników
Wybór odpowiedniej destylarki do rozpuszczalników powinien być dokładnie przemyślany i oparty na kilku kluczowych czynnikach. Po pierwsze, należy określić rodzaj substancji, które będą poddawane procesowi destylacji, ponieważ różne materiały mogą wymagać różnych parametrów pracy urządzenia. Kolejnym istotnym aspektem jest wydajność destylarki, która powinna być dostosowana do potrzeb użytkownika oraz skali produkcji. Ważne jest również zwrócenie uwagi na łatwość obsługi oraz konserwacji sprzętu, co może znacząco wpłynąć na komfort pracy w laboratorium lub zakładzie przemysłowym. Dodatkowo warto sprawdzić dostępność części zamiennych oraz serwisu posprzedażowego producenta, co może okazać się nieocenione w przypadku awarii lub potrzeby modernizacji urządzenia.
Jakie są najczęstsze problemy z destylarkami do rozpuszczalników
Podczas użytkowania destylarek do rozpuszczalników mogą wystąpić różne problemy, które mogą wpływać na efektywność i bezpieczeństwo pracy. Jednym z najczęstszych problemów jest zatykanie się rurki destylacyjnej, co może prowadzić do obniżenia wydajności procesu. Zatykanie może być spowodowane osadami chemicznymi lub zanieczyszczeniami, które gromadzą się w trakcie destylacji. Innym problemem jest nieprawidłowe działanie termometru, co może skutkować błędną interpretacją temperatury wrzenia substancji i prowadzić do nieefektywnej separacji frakcji. Warto również zwrócić uwagę na szczelność połączeń, ponieważ nieszczelności mogą prowadzić do utraty cennych rozpuszczalników oraz zwiększać ryzyko wybuchu lub pożaru. Regularna konserwacja oraz czyszczenie destylarki są kluczowe dla uniknięcia tych problemów.
Jakie są zalety korzystania z destylarki do rozpuszczalników w laboratoriach
Korzystanie z destylarki do rozpuszczalników w laboratoriach niesie ze sobą wiele korzyści, które przyczyniają się do poprawy jakości pracy oraz wyników badań. Przede wszystkim, destylacja pozwala na uzyskanie wysokiej czystości substancji chemicznych, co jest kluczowe w wielu eksperymentach i analizach. Dzięki temu można uniknąć błędów wynikających z obecności zanieczyszczeń, co ma ogromne znaczenie w kontekście badań naukowych oraz przemysłowych. Kolejną zaletą jest możliwość recyklingu rozpuszczalników, co przyczynia się do zmniejszenia kosztów operacyjnych oraz ograniczenia negatywnego wpływu na środowisko. Destylarki umożliwiają także łatwe oddzielanie różnych frakcji substancji, co jest nieocenione w procesach syntezy chemicznej. Dodatkowo nowoczesne urządzenia często wyposażone są w systemy automatyzacji, co zwiększa wygodę użytkowania i pozwala na precyzyjne kontrolowanie parametrów procesu.
Jakie są różnice między destylacją prostą a frakcyjną w kontekście destylarek
Destylacja prosta i frakcyjna to dwa podstawowe rodzaje procesów stosowanych w destylarkach do rozpuszczalników, które różnią się zarówno metodą działania, jak i zastosowaniami. Destylacja prosta polega na jednorazowym podgrzewaniu cieczy i skraplaniu pary w osobnym zbiorniku. Jest to metoda stosunkowo szybka i prosta, jednak jej efektywność ogranicza się do substancji o znacznie różnych temperaturach wrzenia. Z tego powodu nie sprawdza się w przypadku mieszanin zawierających składniki o zbliżonych temperaturach wrzenia. Z kolei destylacja frakcyjna to bardziej zaawansowany proces, który wykorzystuje kolumnę frakcyjną do wielokrotnego skraplania pary. Dzięki temu możliwe jest uzyskanie czystszych frakcji substancji oraz separacja składników o podobnych temperaturach wrzenia. Destylacja frakcyjna jest szczególnie przydatna w przemyśle petrochemicznym oraz farmaceutycznym, gdzie wymagana jest wysoka jakość produktów końcowych.
Jakie są koszty eksploatacji destylarki do rozpuszczalników
Koszty eksploatacji destylarki do rozpuszczalników mogą się znacznie różnić w zależności od wielu czynników, takich jak typ urządzenia, jego wydajność oraz intensywność użytkowania. Podstawowym kosztem jest zużycie energii elektrycznej potrzebnej do podgrzewania cieczy i utrzymania odpowiednich temperatur podczas procesu destylacji. W przypadku dużych instalacji przemysłowych koszty te mogą być znaczne, dlatego warto rozważyć inwestycję w energooszczędne modele lub systemy automatyzacji, które pozwolą na optymalizację zużycia energii. Kolejnym istotnym elementem kosztów są materiały eksploatacyjne, takie jak uszczelki czy filtry, które wymagają regularnej wymiany. Należy również uwzględnić koszty związane z konserwacją urządzenia oraz ewentualnymi naprawami.
Jakie są przepisy dotyczące bezpieczeństwa przy użyciu destylarek
Przepisy dotyczące bezpieczeństwa przy użyciu destylarek do rozpuszczalników są niezwykle istotne dla zapewnienia ochrony użytkowników oraz minimalizacji ryzyka wystąpienia niebezpiecznych sytuacji. Przede wszystkim każda destylarka powinna być używana zgodnie z instrukcją obsługi dostarczoną przez producenta, która zawiera szczegółowe informacje dotyczące bezpiecznego użytkowania urządzenia. Użytkownicy powinni być przeszkoleni w zakresie obsługi sprzętu oraz znajomości zasad BHP związanych z pracą z substancjami chemicznymi. Ważne jest również zapewnienie odpowiedniej wentylacji pomieszczeń, w których odbywa się proces destylacji, aby uniknąć gromadzenia się szkodliwych oparów chemicznych. Należy także stosować odpowiednie środki ochrony osobistej, takie jak rękawice czy okulary ochronne, aby zabezpieczyć się przed kontaktem z niebezpiecznymi substancjami.
Jakie innowacje technologiczne wpływają na rozwój destylarek
Innowacje technologiczne mają ogromny wpływ na rozwój destylarek do rozpuszczalników, przyczyniając się do zwiększenia ich wydajności oraz bezpieczeństwa użytkowania. Jednym z najważniejszych trendów jest automatyzacja procesów destylacyjnych, która pozwala na precyzyjne monitorowanie parametrów pracy urządzenia oraz dostosowywanie ich do specyficznych potrzeb użytkownika. Dzięki zastosowaniu nowoczesnych systemów sterowania możliwe jest osiągnięcie wyższej efektywności energetycznej oraz zmniejszenie ryzyka błędów ludzkich podczas obsługi urządzenia. Kolejnym ważnym aspektem są innowacyjne materiały wykorzystywane w budowie destylarek, które charakteryzują się lepszą odpornością chemiczną oraz termiczną niż tradycyjne materiały. Dzięki temu możliwe jest zwiększenie trwałości urządzeń oraz ich zdolności do pracy z agresywnymi substancjami chemicznymi. Również rozwój technologii odzysku energii pozwala na zmniejszenie kosztów eksploatacji poprzez wykorzystanie ciepła odpadowego generowanego podczas procesu destylacji.
Jakie są przyszłe kierunki rozwoju destylarek do rozpuszczalników
Przyszłe kierunki rozwoju destylarek do rozpuszczalników będą koncentrować się na zwiększeniu efektywności energetycznej oraz zrównoważonym rozwoju. W miarę jak rośnie świadomość ekologiczna, producenci będą dążyć do opracowywania urządzeń, które minimalizują zużycie energii oraz ograniczają emisję szkodliwych substancji. Możliwe jest także wprowadzenie bardziej zaawansowanych systemów monitorowania, które pozwolą na bieżąco analizować procesy i dostosowywać je do zmieniających się warunków. Wzrost znaczenia recyklingu i odzysku rozpuszczalników również wpłynie na projektowanie nowych modeli destylarek, które będą w stanie efektywnie przetwarzać odpady chemiczne. Dodatkowo, rozwój technologii cyfrowych może przyczynić się do integracji destylarek z systemami zarządzania produkcją, co pozwoli na jeszcze lepszą optymalizację procesów.