Budowa maszyn specjalnych to proces, który wymaga zaawansowanej wiedzy technicznej oraz umiejętności inżynieryjnych. Kluczowymi elementami…
Budowa maszyn roboczych
Budowa maszyn roboczych to skomplikowany proces, który wymaga uwzględnienia wielu kluczowych elementów. W pierwszej kolejności należy zwrócić uwagę na konstrukcję mechaniczną, która stanowi fundament każdej maszyny. Elementy takie jak ramy, osie czy wały muszą być odpowiednio zaprojektowane, aby zapewnić stabilność i wytrzymałość. Kolejnym istotnym aspektem jest napęd, który może być realizowany za pomocą silników elektrycznych, spalinowych lub hydraulicznych. Wybór odpowiedniego napędu ma kluczowe znaczenie dla efektywności pracy maszyny. Również systemy sterowania odgrywają ważną rolę w budowie maszyn roboczych. Dzięki nim operatorzy mogą precyzyjnie kontrolować pracę urządzeń, co zwiększa ich wydajność i bezpieczeństwo. Nie można zapominać o elementach zabezpieczających, takich jak osłony czy czujniki, które chronią zarówno użytkowników, jak i samą maszynę przed uszkodzeniami.
Jakie materiały są używane w budowie maszyn roboczych
W procesie budowy maszyn roboczych niezwykle istotny jest dobór odpowiednich materiałów, które zapewnią trwałość oraz funkcjonalność urządzeń. Najczęściej stosowanym materiałem jest stal, która charakteryzuje się wysoką wytrzymałością oraz odpornością na różne obciążenia mechaniczne. Stal nierdzewna jest również popularna, szczególnie w aplikacjach wymagających odporności na korozję. W niektórych przypadkach wykorzystuje się także aluminium, które jest lżejsze i łatwiejsze do obróbki, co czyni je idealnym wyborem dla maszyn mobilnych. Oprócz metali stosuje się również tworzywa sztuczne, które znajdują zastosowanie w elementach mniej obciążonych mechanicznie. Tworzywa te są często używane w systemach izolacyjnych lub jako części osłonowe. Warto również wspomnieć o kompozytach, które łączą właściwości różnych materiałów, oferując jednocześnie lekkość i wytrzymałość.
Jakie są najnowsze technologie w budowie maszyn roboczych
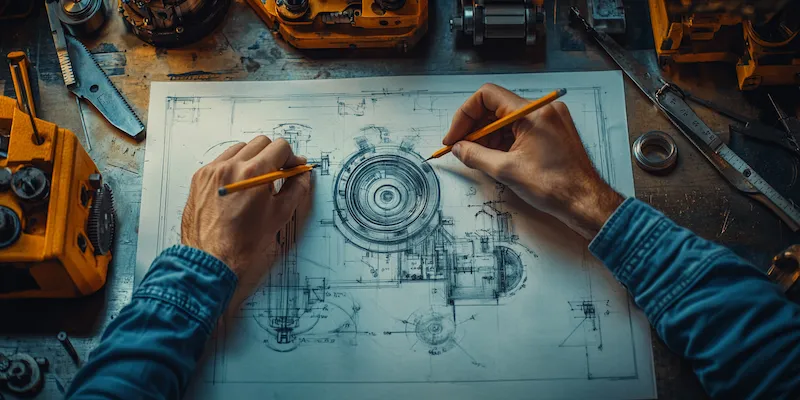
Budowa maszyn roboczych
W ostatnich latach budowa maszyn roboczych przeszła znaczną transformację dzięki wprowadzeniu nowoczesnych technologii. Jednym z najważniejszych trendów jest automatyzacja procesów produkcyjnych, która pozwala na zwiększenie wydajności oraz precyzji wytwarzania komponentów. Roboty przemysłowe są coraz częściej wykorzystywane do montażu oraz obróbki materiałów, co redukuje ryzyko błędów ludzkich i przyspiesza cały proces produkcji. Kolejnym innowacyjnym rozwiązaniem jest zastosowanie druku 3D do wytwarzania prototypów oraz części zamiennych. Technologia ta umożliwia szybkie tworzenie skomplikowanych kształtów przy minimalnych stratach materiałowych. Również rozwój systemów monitorowania i diagnostyki w czasie rzeczywistym pozwala na bieżąco śledzić stan maszyny oraz przewidywać ewentualne awarie. Dzięki temu można zredukować przestoje i zwiększyć efektywność operacyjną.
Jakie są najczęstsze problemy w budowie maszyn roboczych
Budowa maszyn roboczych wiąże się z wieloma wyzwaniami i problemami, które mogą wystąpić na różnych etapach procesu produkcji. Jednym z najczęstszych problemów jest niewłaściwy dobór materiałów, co może prowadzić do awarii lub skrócenia żywotności maszyny. Często zdarza się również, że projektanci nie uwzględniają wszystkich aspektów ergonomicznych, co wpływa na komfort pracy operatora oraz bezpieczeństwo użytkowania urządzenia. Problemy mogą także wynikać z niedostatecznej kontroli jakości podczas produkcji poszczególnych komponentów. Niekiedy występują trudności związane z integracją nowoczesnych technologii do istniejących systemów produkcyjnych, co może prowadzić do opóźnień i zwiększonych kosztów. Dodatkowo zmieniające się przepisy prawne dotyczące bezpieczeństwa maszyn mogą wymuszać na producentach dostosowanie swoich produktów do nowych norm, co również generuje dodatkowe wyzwania.
Jakie są kluczowe etapy w budowie maszyn roboczych
Budowa maszyn roboczych to proces, który składa się z kilku kluczowych etapów, każdy z nich odgrywa istotną rolę w zapewnieniu efektywności i funkcjonalności finalnego produktu. Pierwszym krokiem jest faza projektowania, która obejmuje stworzenie szczegółowych rysunków technicznych oraz specyfikacji materiałowych. W tym etapie inżynierowie muszą uwzględnić wszystkie wymagania dotyczące wydajności, bezpieczeństwa oraz ergonomii. Następnie następuje etap prototypowania, w którym powstaje pierwszy model maszyny. Prototyp pozwala na przetestowanie różnych rozwiązań konstrukcyjnych oraz identyfikację ewentualnych problemów przed rozpoczęciem masowej produkcji. Po zatwierdzeniu prototypu przechodzi się do produkcji seryjnej, gdzie kluczowe jest zapewnienie wysokiej jakości komponentów oraz ich precyzyjnego montażu. Kolejnym ważnym etapem jest testowanie gotowych maszyn, które ma na celu sprawdzenie ich funkcjonalności oraz zgodności z normami bezpieczeństwa.
Jakie są różnice między maszynami roboczymi a urządzeniami przemysłowymi
Maszyny robocze i urządzenia przemysłowe to terminy często używane zamiennie, jednak istnieją między nimi istotne różnice, które warto zrozumieć. Maszyny robocze zazwyczaj odnoszą się do urządzeń zaprojektowanych do wykonywania konkretnych zadań związanych z obróbką materiałów, takich jak frezarki, tokarki czy prasy hydrauliczne. Ich głównym celem jest zwiększenie wydajności produkcji poprzez automatyzację procesów. Z kolei urządzenia przemysłowe obejmują szerszą gamę sprzętu, w tym maszyny robocze, ale także systemy transportowe, urządzenia pomiarowe czy instalacje do zarządzania energią. Urządzenia przemysłowe mogą pełnić różnorodne funkcje, od transportu surowców po monitorowanie procesów produkcyjnych. Warto również zauważyć, że maszyny robocze często wymagają specjalistycznej obsługi i konserwacji, podczas gdy niektóre urządzenia przemysłowe mogą być bardziej uniwersalne i łatwiejsze w obsłudze przez pracowników.
Jakie są najważniejsze normy dotyczące budowy maszyn roboczych
W budowie maszyn roboczych niezwykle istotne jest przestrzeganie odpowiednich norm i standardów, które mają na celu zapewnienie bezpieczeństwa użytkowników oraz niezawodności urządzeń. W Europie jednym z najważniejszych dokumentów regulujących te kwestie jest dyrektywa maszynowa 2006/42/WE, która określa wymagania dotyczące projektowania i budowy maszyn. Normy te obejmują m.in. aspekty związane z bezpieczeństwem mechanicznym, elektrycznym oraz ochroną zdrowia operatorów. Dodatkowo istnieją normy ISO, takie jak ISO 12100 dotycząca oceny ryzyka w projektowaniu maszyn oraz ISO 13849 dotycząca bezpieczeństwa systemów sterowania. Przemysłowe standardy EN są również istotne w kontekście budowy maszyn roboczych, ponieważ dostarczają szczegółowych wytycznych dotyczących różnych typów urządzeń i ich zastosowań. Przestrzeganie tych norm nie tylko zwiększa bezpieczeństwo pracy, ale także wpływa na jakość produktów oraz konkurencyjność firmy na rynku.
Jakie są zalety zastosowania nowoczesnych technologii w budowie maszyn roboczych
Wykorzystanie nowoczesnych technologii w budowie maszyn roboczych przynosi szereg korzyści, które mają znaczący wpływ na efektywność produkcji oraz jakość finalnych produktów. Jedną z głównych zalet jest poprawa precyzji wykonania komponentów dzięki zastosowaniu zaawansowanych narzędzi CNC oraz technologii druku 3D. Te innowacyjne metody pozwalają na tworzenie skomplikowanych kształtów przy minimalnych stratach materiałowych oraz znacznie skracają czas realizacji projektów. Kolejną korzyścią jest możliwość automatyzacji procesów produkcyjnych, co prowadzi do zwiększenia wydajności oraz redukcji kosztów operacyjnych. Dzięki zastosowaniu robotyzacji można również poprawić jakość produktów poprzez eliminację błędów ludzkich podczas montażu czy obróbki materiałów. Nowoczesne technologie umożliwiają także lepsze monitorowanie stanu maszyn dzięki integracji systemów IoT, co pozwala na szybsze wykrywanie awarii i planowanie konserwacji.
Jakie umiejętności są potrzebne do pracy w budowie maszyn roboczych
Praca w budowie maszyn roboczych wymaga szerokiego zakresu umiejętności technicznych oraz interpersonalnych, które są niezbędne do skutecznego wykonywania obowiązków zawodowych. Kluczową umiejętnością jest znajomość rysunku technicznego oraz umiejętność posługiwania się narzędziami pomiarowymi, co pozwala na precyzyjne projektowanie i kontrolę jakości komponentów. Wiedza z zakresu mechaniki i elektroniki jest również niezbędna dla inżynierów zajmujących się projektowaniem systemów napędowych czy sterujących. Dodatkowo umiejętność programowania CNC czy obsługi oprogramowania CAD/CAM staje się coraz bardziej pożądana w branży, ponieważ umożliwia automatyzację procesów produkcyjnych i zwiększa efektywność pracy. Ważne są także umiejętności analityczne i zdolność do rozwiązywania problemów, które pozwalają na identyfikację ewentualnych usterek oraz ich szybką eliminację. Wreszcie umiejętności interpersonalne są istotne dla efektywnej współpracy w zespołach projektowych oraz komunikacji z klientami i dostawcami.
Jakie są przyszłościowe kierunki rozwoju w budowie maszyn roboczych
Przemysł budowy maszyn roboczych stoi przed wieloma wyzwaniami i możliwościami rozwoju w nadchodzących latach. Jednym z kluczowych kierunków będzie dalsza automatyzacja procesów produkcyjnych poprzez wykorzystanie sztucznej inteligencji oraz robotyzacji. Dzięki tym technologiom możliwe będzie osiągnięcie jeszcze wyższej wydajności oraz jakości produktów przy jednoczesnym zmniejszeniu kosztów operacyjnych. Również rozwój Internetu Rzeczy (IoT) otworzy nowe możliwości monitorowania stanu maszyn w czasie rzeczywistym oraz optymalizacji procesów produkcyjnych poprzez analizę danych zbieranych z różnych źródeł. W kontekście ochrony środowiska coraz większą rolę będą odgrywać technologie związane z ekologicznymi rozwiązaniami energetycznymi oraz recyklingiem materiałów używanych w budowie maszyn roboczych. Ponadto rosnące znaczenie personalizacji produktów sprawi, że producenci będą musieli dostosować swoje maszyny do indywidualnych potrzeb klientów, co wymaga elastyczności w procesach produkcyjnych.